數(shù)控機床技術開展淺析。機床既是施行先進制造技術的重要配備,也是制造信息集成的一個重要載體,因而,機床的開展在一定水平上映射出加工技術的主要趨向。在20世紀后期構成的以數(shù)控技術為中心的柔性制造技術,預期在將來仍將持續(xù)停頓并成為加工技術開展的主流。它的特征能夠歸結為3F,3I和3S,即:
由高速切削推進至全面高速化,數(shù)控機床的主軸轉速和功率的大幅度進步為高速切削提供了良好的條件。高速切削的界線,在不同的年代,隨著切削辦法和被加工資料的不同,其數(shù)值也不盡相同,通常以為的高速切削是指比傳統(tǒng)的切削速度和進給速度高出5~8倍。圖1 示出銑削不同金屬資料時的高速切削范圍。而高的進給速度在切削鋼和鑄鐵時可達20~50m/min,相當每個刀齒的進給量為1.0-1.5mm。
顯然高速加工能增大單位時間資料被切除的體積(資料切除率Q),但按目前機床的狀況來看,要充沛發(fā)揮先進刀具的高速加工才能,還必需開發(fā)有更高驅動功率和構造剛度的機床,因而當前航空、汽車和模具等制造行業(yè)普遍地采用高速加工,并不是只限于進步切削效率,還著眼于用它在以下3方面取得對加工質量和經濟效益的提升。
減小切削力,保證薄壁零件加工的外形精度。經過進步切削速度(Vc)和降低進給量(f),在堅持相同資料切除率Q的條件下,使每個刀齒的進給量減小而使切削力降低。
進步加工外表質量。在堅持相同的切削效率(即相同Q值)下,進步切削速度可改善切屑構成過程和增加切削阻尼有利于抑止顫振,而減少每個刀齒的進給量能降低切削外表軌跡構成的殘留高度,改善外表粗糙度,從而有利于精細零件和模具的加工。
減少被加工零件的溫升和熱變形。高的切削速度和低的進給量所構成的連續(xù)切屑流將使更多的切削熱被切屑帶走,減少零件和刀具的熱變形,有利于保證批量消費的零件尺寸穩(wěn)定性。
因而,數(shù)控機床采取進步切削速度和切削進給后,對改善加工質量、縮短切削工時等有明顯的效果,但為了到達機床應用率進一步進步的目的,還需對數(shù)控機床完成全面高速化。對現(xiàn)有數(shù)控機床運用狀況統(tǒng)計得出:其有效切削時間與全部工時之比(機床應用率)僅為25%~35%,其他的75%~65%均耗費在機床調整、程序運轉檢查、空行程、起制動空運轉、工件上下料和裝夾等輔助時間以及待工時間(由于技術準備和調度不及時惹起的非工作時間)與毛病停機時間上。因而需經過進步各軸快移速度和加(減)速度、主軸變速的角加(減)速度、刀具(工件)自動交流速度,改善數(shù)控系統(tǒng)的操作便當性和監(jiān)控功用以及增強信息管理才有可能全面緊縮輔助時間和減少待工時間,使數(shù)控機床的應用率到達60%以上。
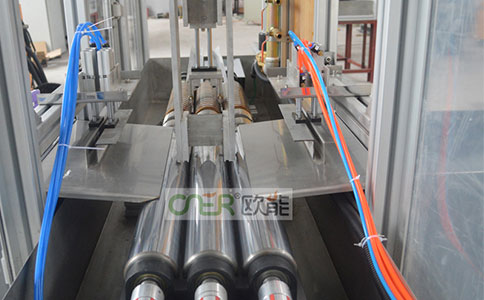